About Us & Our Softgel Manufacturing Process
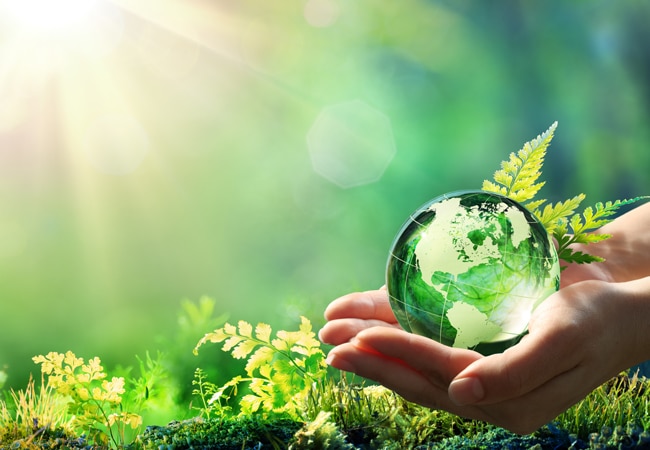
Corporate Conservation
Being a conscious business represents one that demonstrates character—it is authentic, transparent, proactive, and has a
clear set of values.
Soft Gel is proud to contribute to Vitamin Angels’ efforts to create a healthier world for all. Last year alone, they reached over 74 million mothers and children in the US and globally, with life-changing nutrition interventions.
Who We Are
Established in 1994, Soft Gel Technologies, Inc.® (SGTI) is a full-service contract manufacturer of premium-quality soft gelatin capsules exclusively for the dietary supplement industry under the leadership of CEO Ken Tsuchibe.
Our corporate headquarters is located in Los Angeles, California, where our state-of-the-art equipment, professional and well-trained personnel, and exceptional customer service are at your disposal. Our parent company, Japan-based Kenko Corporation, is a trusted global supplier of high-quality functional ingredients across various industries, including dietary supplements, cosmetics, foods and beverages, animal feed, and life sciences.
Thanks to our unique East-West fusion, SGTI combines the best of American technology with the innovations of Japanese genius to deliver unmatched precision in manufacturing and groundbreaking excellence in product formulations.
You can count on us to effectively meet your encapsulation needs in a reliable manner.
- We produce and market branded products and turnkey custom formulations.
- We specialize in creating unique, high value supplements.
- We focus on ingredients that are difficult to encapsulate, fragile to work with, or difficult to absorb.
- We offer numerous exclusive ingredients for softgel applications, many of which are patent-protected.
- We develop new technologies that enhance nutrient bioavailability and functionality over traditional delivery systems.
Our Capsule Manufacturing Company’s History
Since our inception, we have maintained our goal of providing high value-added products. Specifically focusing on ingredients that are difficult to absorb, difficult to encapsulate, or fragile to work with, we have developed an array of proprietary technologies that allow our products to deliver superior results. We have earned many U.S. patents, most of which are for significant technological breakthroughs in the area of nutrient bioavailability.
Soft Gelatin Capsule Services
When you partner with us, we can assist with research, real-time stability data, and marketing resources. We have access to a portfolio of unique ingredients from around the globe. Having an international sales team enables us to export our softgels throughout the world. We support our exclusive products through clinical studies, extensive marketing and educational efforts. We are committed to helping customers effectively communicate the benefits of our products and be a reputable source of information.
Given the increasing globalization of the multi-layered supply chain, we understand the challenges of identifying safe and pure ingredients that we can reliably utilize in our products. We achieve these through a combination of extensive testing, thorough supplier qualification, and ingredient traceability.
Our Solvent-Free Manufacturing Plant
All of the premium supplements manufactured by us are produced on-site in a world-class facility. We have set the “gold standard” when it comes to the manufacturing of soft gelatin capsules. Each batch is manufactured according to current Good Manufacturing Practices (GMPs) for dietary supplements. Quality is constantly monitored during every step of the manufacturing process to achieve the highest level of technical excellence in softgel production.
We have invested millions of dollars to purchase precision, state-of-the-art blending, and encapsulation equipment, which enable us to consistently manufacture the finest softgels for our customers. The encapsulation and inspection processes occur in temperature-controlled areas. We have automated many of the inspection and packaging processes with precision equipment designed to FDA 21 CFR (Code of Federal Regulations) Part 111 requirements, which helps increase throughput. We embrace corporate transparency through our meticulous quality assurance procedures and comprehensive QC testing.
Softgel production is a very unique and complicated process; not every manufacturer can do it. While softgels can be difficult to manufacture because water-soluble/hydrophilic materials are not easily encapsulated and the operators who run the encapsulation machine have to be well-trained and competent to learn the techniques for smooth and efficient operation, we have innovated ways to overcome these challenges. We specialize and thrive in encapsulating formulas that others thought weren’t possible in softgels. We have a production team who, with high precision and constant oversight, monitors and controls the gelatin temperature, ribbon thickness, seam width, and fill quantity during manufacturing.
In-House Analytical Laboratory
One of our strongest company attributes is our well-equipped, state-of-the-art, chemical analytical laboratory and the staff who run it. Highly-trained chemists and technicians create an environment of product integrity with complete confidentiality and full compliance with state and federal regulations. All work performed in our lab facility is in accordance with current Good Laboratory Practices (cGLPs). Our sophisticated laboratory instruments exceed industry standards, are subject to annual Operational Qualification/Performance Verification, and are 21 CFR Part 11 compliant.
Quality Control (QC) provides testing through all stages of production, from incoming raw material testing and identification, in-process quality checks, and final product testing for potency and quality of the products we manufacture. QC uses state-of-the-art instruments such as:
- High-Performance Liquid Chromatography (HPLC)
- Gas Chromatography (GC)
- Atomic Absorption (AA)
We use independent third-party testing laboratories since they offer unbiased analytical testing to support the quality of our products and meet customer requirements. These labs are an extension of our in-house laboratory. We qualify each of our third-party labs by verifying their data is technically sound, ISO/IEC 17025 accredited, and cGMP and GLP compliant.
When you partner with us, we can assist with real-time stability data. We highly encourage our customers to perform regular audits of our facility, where they can look at batch records, raw material certificates of analysis, and ensure that we are doing all of the testing required for GMP compliance.
Corporate Conservation
We are committed to sustainability and practice corporate conservation. Here’s how we’re reducing our environmental footprint:
- We produce our own energy
- We are a solvent-free facility
- We strive towards lean manufacturing—zero waste
- We sell remnant gelatin to scrap gelatin processors for use in adhesives
- We use energy-efficient LED lighting and motion sensors in our facility
- We recycle paper
- We utilize earth-friendly cleaning products
Soft Gel is proud to contribute to Vitamin Angels’ efforts to create a healthier world for all. Last year alone, they reached over 74 million mothers and children in the US and globally, with life-changing nutrition interventions.
Building a Greener Future One Kilowatt-Hour at a Time
We have incorporated a 260-kilowatt co-generation machine that generates electricity using natural gas. When the power is generated, heat is produced and can be harnessed for other elements, such as heating water for our boiler. We also have invested in two additional chiller units (45 and 75 tons, respectively) as part of our manufacturing capabilities. This eco-friendly upgrade to our facility supplies us with an uninterrupted source of power, independent of the California Power Grid. By providing 80% of our own power, we can be considered a reliable and environmentally-conscious supplier.
- We reduce air pollution by recycling the waste heat.
- We save other pollutant-spewing fossil fuels from being burned.
- We cut carbon dioxide emissions, other greenhouse gases, and nitrogen oxides.
Reducing Waste in the Workplace
By adopting a strategy of lean manufacturing and green thinking, we have streamlined our production process and are utilizing our resources more efficiently. We are committed to saving more than just trees. We have reduced the amount of gelatin left over from each manufacturing run and sell the remnants to other industries, so that there is less waste.